后處理吹氣式液位計由過濾減壓閥、吹掃裝置、差壓變送器及中間連接管線等組成,由昌暉儀表制造有限公司在出廠時集成在一起,現場施工只連接氣路管線即完成安裝,使安裝難度下降。
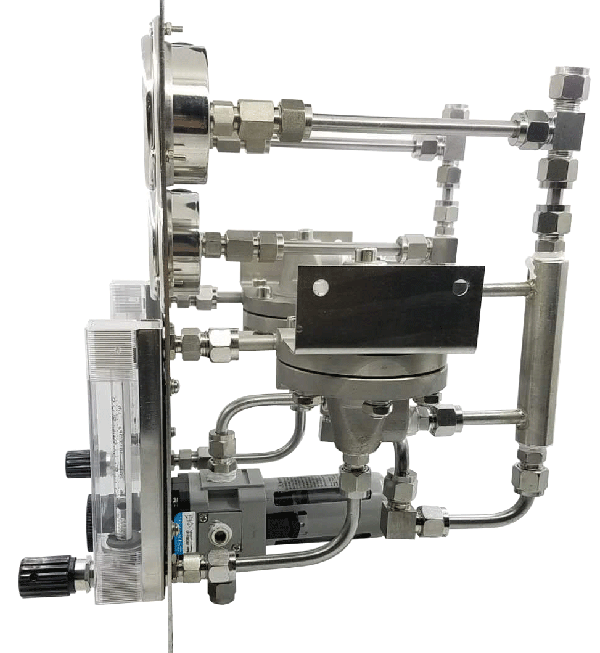
1、混合澄清槽吹氣儀表檢測方案
1.1 吹氣檢測原理
吹氣式液位計主要由兩部分構成,一部分為吹掃裝置,由空氣過濾減壓閥、小流量控制器與玻璃轉子流量計構成,另一部分由差壓變送器、波紋管防污隔離閥(根閥)和伸入設備的吹氣管組成,其工作原理如圖1。吹氣檢測方法是將吹氣管插入到設備的不同深度,然后將壓縮空氣通過過濾減壓閥后,均勻地進入吹氣管中,連續不斷地向被測介質中吹入。當吹氣管下端液面位置的靜壓小于吹氣管內的壓力時,壓縮空氣經吹氣管下端的氣泡均勻冒出,差壓變送器上獲得的差壓值即為兩根不同深度的吹氣管對應位置的靜壓值,根據設置的吹氣管插深和差壓值,獲得需檢測的各參數。基本公式為p=ρgh,其中ρ為容器內介質密度,g為重力加速度,h為吹氣管插入的深度。
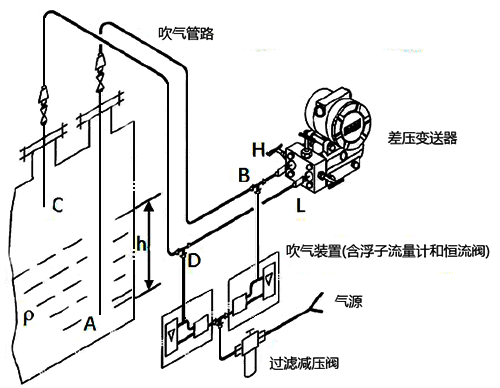
圖1 吹氣式液位計測量原理示意圖
1.2 混合澄清槽吹氣儀表檢測方案
混合澄清槽是后處理溶劑萃取生產過程中用到的一種溶劑萃取裝置,依靠重力來實現水相和有機相的混合和澄清分相,通過對混合澄清槽的界面、液位、密度等參數的測量監控運行狀態,為運行人員提供有效數據。各混合澄清槽的尺寸和級數不盡相同,但是每級檢測的工藝參數相同。
在建后處理項目中的混合澄清槽需檢測兩級相關參數的,每級檢測的參數均為水相密度、有機相密度、液位和界面,采用吹氣測量法進行檢測。測量裝置由吹氣管、吹掃裝置和差壓變送器3部分構成,檢測到的差壓信號送至控制系統運算后顯示。但是,其檢測系統的設計有兩種,如圖2所示。一種是由二管、三管和四管3個分體式吹氣儀表組合使用方式,另一種是由三管、四管和四管的分體式吹氣儀表組合使用方式,都能夠滿足工藝參數的測量。

圖2 現有混合澄清槽儀表檢測系統
同一級設備檢測的參數相同,第一級插管數量均為5根,第二級插管數量均為4根,第一級與第二級之間共用吹氣管,但是吹氣儀表的組合使用方式,因設計人員的不同而具有差異性。該種方式存在結構零件及管線較多,安裝空間占地大,維護檢修工作量大等問題。隨著項目的開展,核化工儀控設計人員結合科研成果,在項目中開始部分使用由生產廠家集成好的吹氣式液位計,一定程度上改善了吹氣儀表的外形,使其更加緊湊,所占空間更小,同時管線系統的改進與集成使安裝難度下降。但是,工藝關鍵設備使用的吹氣儀表結構形式仍為分體式,各子項間對同種關鍵設備和相同的檢測參數,選用的吹氣式液位計也不盡相同,同時在安裝過程中,管線之間的連接和差壓檢測儀表的安裝仍然存在安裝困難的問題。
2、混合澄清槽配套吹氣式液位計檢測方案設計
2.1 混合澄清槽配套吹氣式液位計儀表管線系統優化及整體方案設計
在分析總結后混合澄清槽及其吹氣儀表檢測情況的基礎上,結合現有吹氣式液位計研究成果,優化改進管線系統,把兩個及兩個以上的吹氣裝置內的管線系統集成到一個吹掃裝置中,同時將吹掃裝置、壓力/差壓變送器及其連接管線整合為一體,對管線進行集成化、一體化設計,設計混合澄清槽配套吹氣式液位計檢測統一化、標準化的檢測方案。
圖2為現有混合澄清槽儀表檢測系統,均有兩級需要檢測,由3個吹掃裝置共同測量。吹掃裝置雖然組合方式不同,但是每一級的檢測參數均相同,獲取密度、液位等8個工藝參數,然后通過壓力變送單元就地顯示壓力差。因此,可研究每一級設備單獨的吹氣管線系統方案,減少各級之間共用的吹氣管,使每一級管線系統相對獨立,將吹氣管線系統氣路分配去復雜化,吹氣管線系統優化后如圖3所示。每一級設備內插入5根吹氣管,將兩級之間的共用管分別每級單獨配置,相較于原氣路分配,兩級及以上的混合澄清槽氣路管線系統,每增加一級,多一根吹氣管,但是每一級的檢測系統相對獨立,互相無影響,可以降低管線系統氣路分配的復雜性,實現每級液位、界面、水相密度和有機相密度的4個參數的檢測。
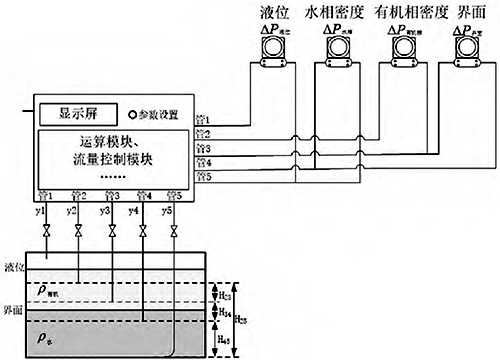
圖3 混合澄清槽每級管線系統優化檢測方案
將混合澄清槽原有的兩個及兩個以上吹氣式液位計及復雜的儀表管線系統優化,對管線進行集成化、一體化、標準化設計的過程中,管線系統內部結構的復雜性上升,因此儀表部分需具有一定的靈活性,對其進行模塊化設計,方便后續維護和零部件的更換。在優化吹氣管線系統的基礎上,將測量部件(壓力傳感器、信號處理模塊、運算模塊、顯示模塊及電源模塊)、取壓部件(取壓分配器、流量控制器、過濾減壓裝置及吹氣管管路系統等)模塊化后,將吹氣裝置和8個變送器集成在一個箱體式的吹氣式液位計中,形成針對混合澄清槽的專有一體化吹氣檢測系統的總體設計方案如圖4所示。
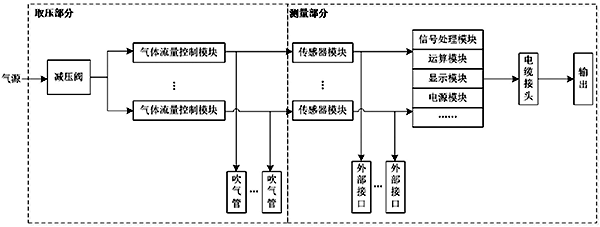
圖4 混合澄清槽配套吹氣式液位計儀表方案原理框圖
其中,氣體流量控制模塊將浮子流量計和穩流閥設計成模塊化形式,方便拆裝,將吹氣流量控制在0L/h~10L/h的范圍內,具體的調節在調試過程中,通過氣體流量控制模塊上的旋鈕對氣體流量進行調節,以使氣體在吹氣管口能夠穩定、均勻地冒出氣泡,平均速度為1個/秒。
2.2 混合澄清槽配套吹氣式液位計檢測系統運算方案研究
混合澄清槽配套吹氣式液位計檢測運算是將差壓值轉換為液位、密度、液位信號、界面等檢測參數,具體需根據吹氣管浸入的位置對各參數進行計算。設管1、管2、管3、管4和管5分別為y1、y2、y3、y4和y5。
當液位穩定在混合澄清槽溢流堰口時,存在關系:?P液位=?P界面+P1,其中?P液位和?P界面分別為變送器的實測值,P1為y2管的理論壓力值。下面根據y2管末端位置進行判別,并給出具體運算公式。
①當?P液位≥?P界面+P1+X時,液位穩定在溢流堰口,或高于溢流堰口,即y2管末端浸入有機相中。其中,X為修正系數,可根據調試情況修改。
此時,液位為:
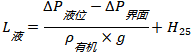
H25為y2管、y5管管間距。
此時,界面為:
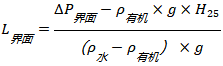
②當?P液位≤?P界面+P1+X,液位發生下降,低于溢流堰口,y2管末端已經暴露于氣相中,此時工況異常,無法精準計算液位。
對液位進行估計:
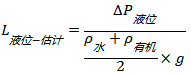
當L液位-估計≥H25時,L液位≈H25;當L液位-估計≤H25時,L液位≈L液位-估計。
對界面范圍的估計,需借助?P水相,根據每個周期的數據變化來判斷,界面位于y4管以下,還是y2管與y4管之間。
③有機相密度與水相密度的計算
當液位高于y2管,界面低于y3管,即y2管與y3管末端均浸入有機相中,此時可測得有機相密度ρ有機=?P有機/(H23×g)。當界面高于y4管時,ρ水=?P水相/(H45×g)。
為了獲得液位、界面的更大有效測量區間,兩密度實測值不參加液位、界面運算,公式中使用的密度為給定值。
3、結論
本文基于混合澄清槽設備自身特點和檢測需求,結合吹氣測量法,優化吹氣管線系統,將每一級吹氣管線獨立化設計,減少了吹氣管線系統的復雜性,然后給出吹氣式液位計集成化、模塊化設計原理圖,方便后續維修和零部件的更換。最后,給出根據差壓值轉換為液位、密度、液位信號、界面等檢測參數的運算方案。混合澄清槽配套吹氣式液位計檢測方案可減少現場的安裝、維修工作量,節省安裝空間,降低了一定的經濟成本,同時利于核化工項目設計的統一化,也可減少現場備品備件的種類,增強零部件的通用性。
作者:楊佳煜、趙利美、王志勇
相關閱讀
◆四張圖弄懂吹掃裝置典型應用