隨著我國電力事業的發展,大容量、高參數的1000Mw等級的超超臨界機組應運而生并呈快速發展之勢。熱控專業在設計過程中遇到了新的難題,1000MW超超臨界機組熱電偶選型便是其中之一,如何適應超高參數機組測溫的要求值得專業人員深入的思考和研究。
1、超超臨界機組對測溫熱電偶選型的影響
超超臨界機組工藝參數大幅提高,以鄒縣電廠四期工程1000MW機組為例:
①過熱器出口額定蒸汽壓力為26.25MPa,額定蒸汽溫度為605℃;
②再熱器出口額定蒸汽壓力為4.9MPa,額定蒸汽溫度為603℃;
③高壓加熱器出口給水壓力為33.3MPa,溫度為298.8℃。
為適應如此高的溫度和壓力條件,管道材質發生了變化,如主蒸汽管道采用A335 P92,再熱熱段采用A335 P91,主給水管道采用15NiCuMoNh5(WB36)
2、超超臨界機組熱電偶保護套管材質的選擇
熱電偶保護套管材質的選擇要考慮被測介質的壓力、溫度、流速、流體激振頻率,輸送介質的管道材質,以及保護套管本身的耐溫耐壓能力,材料的焊接特性、熱膨脹特性、振動頻率等相關特性。對熱電偶保護套管材質的選擇,鄒縣四期工程設計中提出了兩種方案,即采用與工藝管道同材質方案和采用不銹鋼材質方案。
2.1 采用與工藝管道同材質方案
采用與管道同材質的熱電偶套管方案,無疑是最簡單、最可靠的,它同時滿足了溫度、壓力、焊接等方面的要求。但該方案也存在著缺陷,因為無論是P91還是P92材質都會生銹,在使用一段時間之后,超超臨界機組熱電偶會銹死在套管里,若熱電偶出現故障,需要更換時無法取出,則必須重新開孔安裝;如果該溫度信號用于調節系統,就會給運行帶來很大的不便。
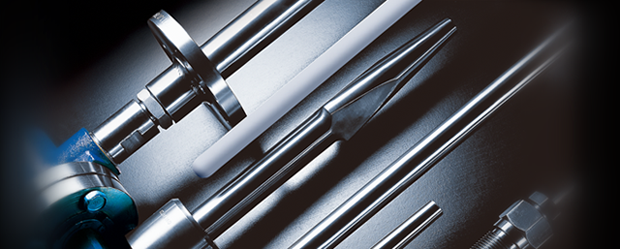
在亞臨界機組上電站專用熱電偶套管全部采用1Crl8Ni9Ti不銹鋼材質套管,熱電偶的更換十分方便,經過多年的實踐運行,證明是可靠的。那么,能否同樣采用1Crl8Ni9Ti不銹鋼材質做超超臨界機組熱電偶呢?
為此,需解決以下幾方面的問題:
2.2.1 1Crl8Ni9Ti不銹鋼材質在超超臨界參數下的耐溫耐壓特性在華電國際鄒縣發電廠四期工程熱電偶選型過程中,超超臨界機組熱電偶生產廠給予了積極配合,并對采用1Crl8Ni9Ti不銹鋼材質的方案,提供了理論計算依據。計算條件如下:
①分析對象。熱電偶套管,材質為1Crl8Ni9Ti。
②固定方式。根部焊接固定連接。
③分析方法。有限元ANSYS 5。
④計算參數。溫度610℃,壓力40MPa,流速100rn/s。
計算結果:頻率安全系數為3.3(一般1.5-2即可),推力系數為7.8(一般3-5即可)。通過計算1Crl8Ni9Ti不銹鋼材質,完全可以滿足超超臨界機組的運行參數。
2.2.2 1Crl8Ni9Ti不銹鋼材質與P91、P92管道的異種鋼焊接問題
套管材質確定后,就需考慮異種鋼的焊接問題,四大管道配管廠表示此類焊接問題完全可以解決,并可實現工廠化。另一方面,鍋爐廠、電建公司等單位也掌握了該類焊接技術,并在工程實踐中成功實施。因此,在異種鋼焊接技術上不存在問題。
2.2.3 熱膨脹問題
除此之外,還有一個疑問,1Crl8Ni9Ti不銹鋼材質的熱膨脹系數大于P91、P92材質,在機組運行中會產生熱膨脹應力,是一個潛在的不確定因素,但該影響究竟有多大,目前還沒有可靠的數據。在常熟、沁北等超臨界機組上采用了1Crl8Ni9Ti不銹鋼熱電偶套管,管道材質為P91,并已成功投運2年多,而P91、P92在焊接和熱力特性上相似。由此可見,在超超臨界機組上采用1Crl8Ni9Ti不銹鋼熱電偶套管也是可行的,鄒縣四期工程最終確定采用1Crl8Ni9Ti不銹鋼材質的超超臨界機組熱電偶套管。
熱電偶套管采用與管道同材質或不銹鋼材質,哪一種方式更合理,還需要通過實際運行來檢驗。
3、超超臨界機組熱電偶的安裝方式
在超高參數管道上必須采用可靠的焊接方式以保證設備安全,根據熱電偶選型的不同,其焊接方式也不同。
3.1 管道直接焊接方式
管道直接焊接方式是直接在管道上開孔、打坡口,熱電偶與管道完全焊接,如下圖所示,這種焊接方式的優點在于焊接面幾乎與管道壁厚相同,焊接非常牢靠,介質沖擊力完全在管道壁上。當熱電偶套管受熱膨脹時可沿上、下兩個方向自由膨脹,減少了熱應力沖擊。鄒縣四期工程在設計院設計范圍內的所有四大管道上的熱電偶均采用這種焊接方式。
3.2 帶管座的熱套式焊接方式
下圖為熱套式管座焊接方式,先在管道上開一個640mm的孔,然后在管道壁上焊一個8.9mm×23.5mm的管座,再將熱電偶插入管座內,將熱套式熱電偶套管與管座焊在一起。這種焊接方式適用于熱套式熱電偶,它對管座制作及熱電偶焊接過程要求非常嚴格,必須同時滿足下列條件:
①管座焊接時,必須保證管道開孔與管座同心。
②熱電偶焊接過程中必須保證熱電偶完全卡在640mm的孔上,這樣才能保證受力點在管道內壁上。
③熱電偶與管座之間須保證有3mm左右的間隙,才能焊接。
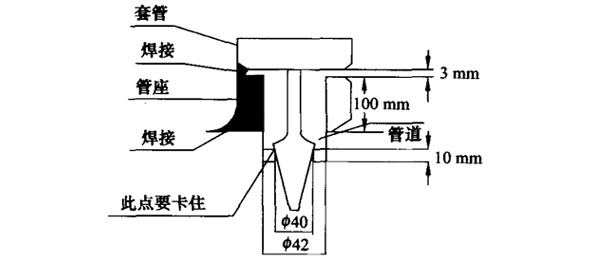
這種焊接方式存在著難以克服的缺點,如超超臨界機組管壁厚,過熱器出口可達85mm,加上100mm的管座,其允許的加工誤差已經大于熱電偶與管座之間3mm左右的焊接間隙要求,再加上管道開孔與管座的同心度偏差等因素,無法保證熱電偶套管完全卡在640mm的孔上,這樣,會造成熱電偶的受力點由管道內壁變為熱電偶與管座焊接處,使沖擊力矩變大,很容易在熱電偶與管座焊接處斷開。
另一方面,當熱電偶套管受熱膨脹時,在管道內壁及管座焊接處兩個點受到限制,膨脹的空間小,會產生較大的熱應力。
鑒于以上原因,在超超臨界以及超臨界機組上不推薦采用管座式焊接方式。
4、超超臨界機組熱電偶插入深度的確定
超超臨界機組的管道直徑大,如主汽管道達到了548mm,給水管道達到了660mm,在超高溫高壓條件下,熱電偶套管承受巨大的推力,在同一管道內,熱電偶插入長度增加100mm,對溫度測量結果的影響遠小于由此產生的大力矩帶來的潛在危險,因此,其熱電偶插入深度不能太長。
另外,高流速管道中的介質運動呈趨壁效應,其介質密度在靠近內壁處比中心軸線處高得多,所以測量介質的溫度應該靠近管壁。
因此,通過計算,在超超臨界機組中,主蒸汽、給水、冷段、熱段等管道溫度的測量,超超臨界機組熱電偶的插入深度均按100mm考慮,這樣既利于溫度測量又保證了安全性,簡化了超超臨界機組熱電偶選型。